Docklands Light Rail
BarChip Fibre Reinforced Concrete Track Slab
BarChip Fibre Reinforced Concrete Track Slab
The Docklands Light Railway in London, UK, was the first macro synthetic fibre reinforced concrete track slab in Europe. Completed in 2005, The Docklands Light Rail extension was a 4.4 km, twin track extension from Canning Town through North Woolwich to London City Airport. Due to urban congestion two-thirds of the track, along with 4 new stations, had to be build on an elevated viaduct. The viaduct consisted of post-tensioned concrete segments with spans of up to 37m.
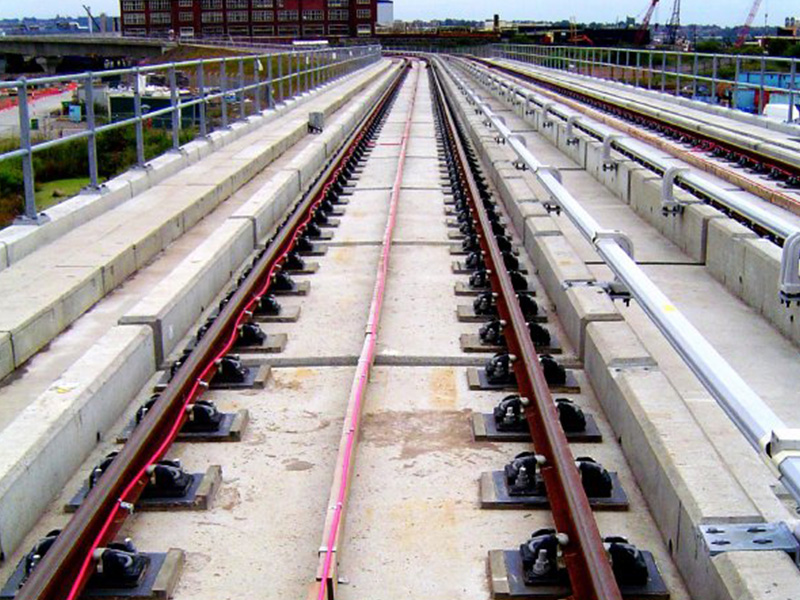
Elevated Section BarChip Fibre Reinforced Concrete Track Slab
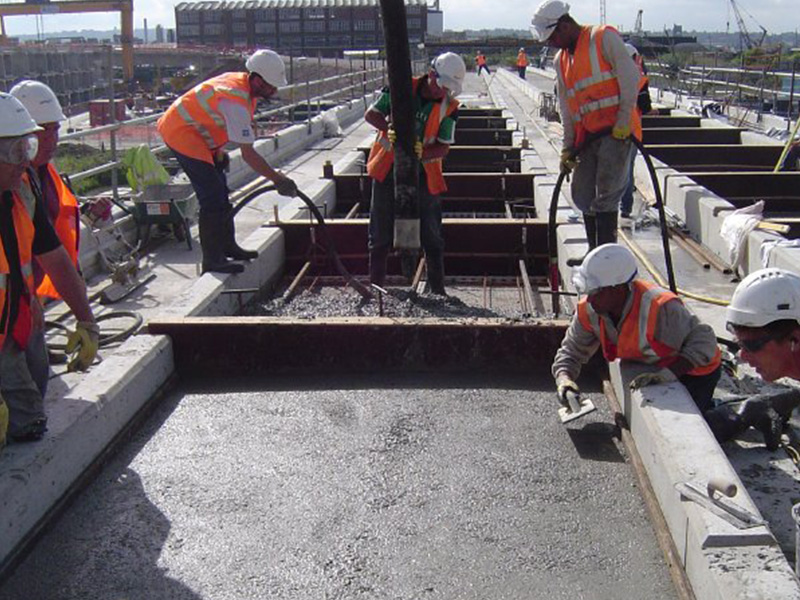
Pumping fibre reinforced concrete track slab
The project adopted a concrete track slab to reduce maintenance, weight and construction depth and to allow up-stands for use as derailment containment. A third-rail system was used for return traction current which increased the potential for stray current corrosion. Reinforcement was required to avoid early-age thermal cracking of the infill trackslab. However, traditional steel reinforcement would increase the risk of circular currents which would interfere with the automatic train-control system.
Full scale site trials were undertaken to test synthetic fibre reinforced concrete which resulted in BarChip fibre being selected at a dose rate of 6 kg/m3. The trackslab was cast in standardised 2.4 and 2.5 m bays using a concrete pump for placement, with BarChip fibre reinforced track slab used across the entire 4.4 km extension. A further extension through King George V to Woolwich Arsenal under the river Thames was completed in 2009. BarChip fibre reinforced concrete was again chosen for the trackslab reinforcement.
On this extension, the Barchip fibre reinforced concrete mix was pumped 1500 m through the newly constructed tunnels.

Trial pour BarChip fibre reinforced concrete track slab
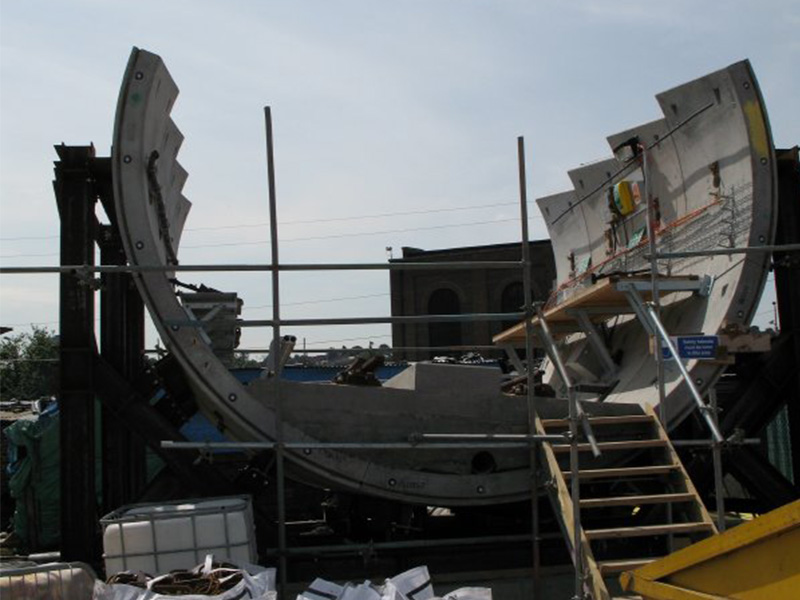
Concrete track slab trial pour in tunnel segment section
15 Year Inspection of Fibre Reinforced Concrete Track Slab
15 years after the initial extension and half way through the 30 year design-build-finance-maintain contract, the BarChip fibre reinforced track slab continues to perform strongly, with no major concerns or defects reported. The use of BarChip on the project not only reduced the risk of circular currents, it also saved significant construction time by eliminated installation of traditional reinforcement and improved the ductility performance of the structure.
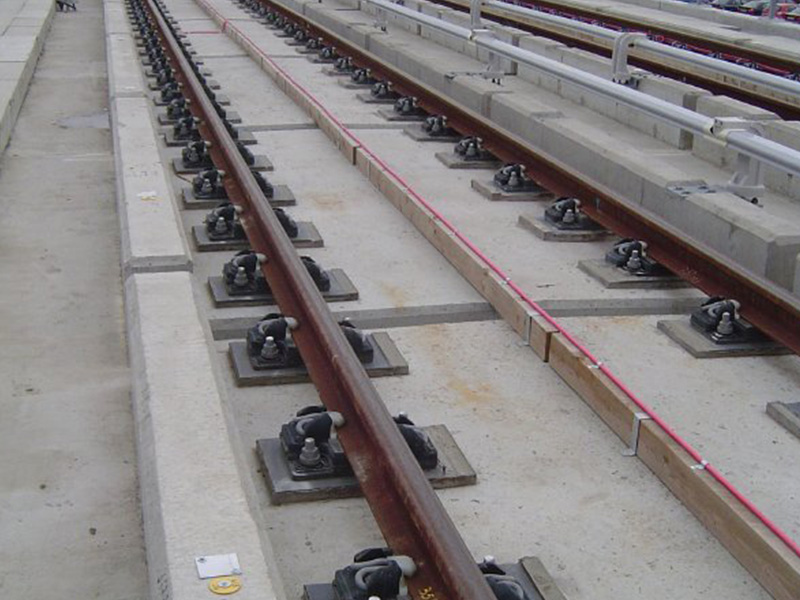
Rail fixings to fibre reinforced concrete track slab